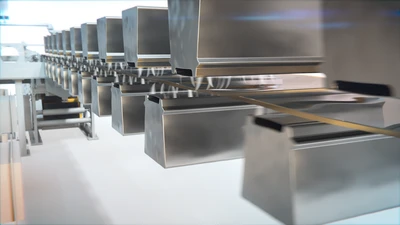
Simultaneous two-sided electrode coating
Aug 6, 2020
Advancing battery electrode development and manufacturing
Dürr Megtec is continuously advancing battery electrode development and manufacturing. Eric Maki, Development Center Manager, and David Ventola, Director Business Development- Engineered Products, both with Dürr’s Clean Technology Systems (CTS) division in De Pere, WI, USA are in the mid of the research process for improved equipment and process solutions in the growing battery business. For them Dürr Megtec’s two-sided coating machines, available in various sizes, offer higher electrode quality and lower operational costs than other players in the market.
The electrode “technology inside” every lithium-ion battery, whatever it powers, is metal foil that is coated on both sides with a special chemical mixture/slurry. The foil material is aluminum for the positive electrode and copper for the negative electrode. These coated electrodes make the battery work, so if the coating is not right, the battery will not be right and could fail. This is why the entire coating process is extremely precise and tightly controlled.
A typical coating chemistry is lithium salts dispersed in an electronics-grade solvent and graphite dispersed in water. The mixture is applied to both sides of the foils with a device called a slot-die. The foil travels over a stainless steel backing roll that helps control the foil and provide a solid platform for producing an accurate wet coating layer. Optimum battery performance requires controlling every step in the coating process, from powder handling and slurry mixing to coating and drying. However, the key challenge of slot-die coating against a backing roll occurs when applying the chemistry to both sides of the foil.
The usual process only allows coating the foil one side at a time. This production set up requires two separate passes through the same coating line, but a more efficient method is to coat both sides in a single pass. Two ways to do this include: 1) with a sequential or tandem coating system or 2) with simultaneous two-sided coating.
Eric Maki, Development Center Manager, Dürr - Clean Technology Systems (CTS)
Dürr Megtec engineers in De Pere decided for the latter: They developed a tensioned-web coating process using a slot-die mounted in a vertical orientation to simultaneously coat both sides of electrode foil traveling horizontally. The process delivers a uniform coat weight matched to that of backing roll coating.
The promise of simultaneous two-sided coating for battery manufacturers is the ability to enhance production efficiencies. Benefits of simultaneous two-sided electrode coating include:
- Effectively double the throughput compared to single-side coaters
- Requires only one pass through the dryer, delivering equal drying of both coated sides
- Smaller overall manufacturing footprint compared to tandem lines–the overall length is 5 to 10 meters shorter, and the height is 5 to 6 meters less
- 30 percent to 50 percent lower capital and operating costs compared to tandem coating lines
- Increased range of coat weights for lithium-ion slurries
- Reduced incidents of particles being trapped at the coating point (no streaks or no foil breaks)
- Fewer problems with wrinkles at the coating point
Enhancing efficiencies, increasing yields, and improving end-use performance
The energy storage industry is demanding reduced production costs along with increased yields and product quality. However, manufacturing large quantities of lithium-ion battery cells requires a significant change and dimensional upscaling of the production equipment and output per line to achieve industry targets. At the same time, the benefits of our two-sided simultaneous coating technology become increasingly important the wider and faster coating lines are required to get.
David Ventola observed that this speed to market is why battery manufacturers are turning to Dürr Megtec for solutions to speed the transition from R&D to mass production of lithium-ion battery electrodes.
We offer a suite of coating lines. From an easy-to-use laboratory coating line designed specifically for short production runs, to the GigaCoater™ system that can provide an annual output of 2 to 3 gigawatt hours (GWh) per machine.
David Ventola, Director Business Development- Engineered Products, Dürr - Clean Technology Systems (CTS)
In other words: that is enough battery electrode capacity to provide 5 hours of backup power for 300,000 homes (based on average consumption of 2kWh), or energy storage for 30,000 battery electric vehicles (100 kWh configured vehicle). As the lithium-ion battery industry matures, pressure to decrease costs continues to mount. Our simultaneous two-sided coating process enables battery manufacturers to be more cost-effective, and therefore, more competitive. By shortening the time it takes to get lithium-ion batteries to market, manufacturers are not delayed in getting their battery-powered products into the hands of their customers. Dürr’s capabilities are helping battery manufacturers grow their business by meeting the growing demand of end-use applications for lithium-ion batteries. Therefore, the next time you use a battery-powered device, most likely later today, remember–Dürr is part of the “technology inside.”
Find out more about lithium-ion battery electrode manufacturing.