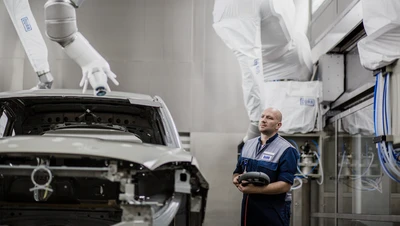
Virtual calculation of layer thicknesses
Nov 20, 2020
Digital twin simulates layer thicknesses directly in the spray booth
Uniform layer thicknesses are an important quality factor in industrial car painting. Until now, perfect painting results were achieved after running multiple tests. With the newly developed software, Dürr has now created a possibility to calculate layer thicknesses virtually and reducing the number of real-life tests tremendously. The new software will be incorporated into the existing programming software of our application robots. First beta site versions are already in use.
The adjustments that need to be done for new projects in a paint shop, for example when a new model is launched, are sensitive to changes, require numerous tests until the results are perfect and are therefore costly and not very environmentally friendly. With the new simulation tool from Dürr, manufacturers can now model and optimize this process virtually.
It is now possible to reduce the number of test paint runs and test bodies by more than 50%,” explains Dr. Lars Friedrich, President & CEO Application Technology at Dürr Systems AG. “This makes commissioning more efficient, lowers material costs, and results in fewer poorly coated bodies.
On the path to a fully digitalized paint shop, this is one of many important steps. Computer-assisted products and process developments make painting processes more economical. Simulating different steps of the painting process helps optimizing before the first prototype goes into production. Using qualified calculations, they anticipate where any problems might occur and provide remedies prior to manufacturing. Especially challenging parts, like joints in the trunk of a car, can be calculated a lot more precisely than it used to be with traditional testing.
The new →DXQ3D.onsite module is based on three steps. It firsts calculates how much paint is applied at any points using idealized, virtual spray patterns that are close to actual conditions. The spray patterns can be scaled dynamically in height and widths. Playing with these two parameters, the user can simulate what effect different spray patterns might have on the layer thickness distribution.
At Dürr’s Digital Factory, a cross-departmental software competence center, around 100 experts work on innovative and tailor-made applicationssolutions for operation, analysis and control of the plants. Find out more about our → DXQ software products.
To model the reality in advance on the computer, the software module creates a digital twin of all key individual components in the form of electronic data. During the first simulation, the tool creates its own 3D file of the body. It only uses information that is relevant for the simulation which saves storage space. Therefore, the program can be used on a notebook directly at an operating spray booth. The module also has very short calculating times that make it possible to simulate the paint layer thicknesses off complete bodies on a conventional PC and not a mainframe computer.
This makes it easy to assess the quality of paint layer thicknesses, better interpret coating results, and optimize neuralgic zones with inconsistent layer thicknesses,” says Frank Herre, Head of Application Process Development at Dürr Systems AG.
Once all the relevant data is merged for the final time, a virtual spray pattern along the robot paths programmed off-site is produced. It adds up the layer thicknesses and displays them in a 3D paint map. Optimization solutions are visualized in a transparent way and can be taken into consideration by the team and improved prior to production.
The second step of the process simulation includes a test in the Dürr laboratory. The software does not take into account specific paints. The customers’ chosen paint materials are used in this real life test at Dürr. In the last step, the virtual parameters and real life results are translated into parameters for the paint atomizer. The first real-life test painting is then carried out with pre-optimized conditions and parameters.