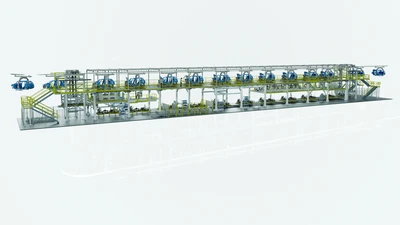
NEXT.assembly: NEW TRENDS WITH FLEX DECKING
Nov 17, 2020
Modular assembly system provides the highest flexibility
With flex decking the Italian Dürr subsidiary CPM S.p.A. invented a modular assembly system for medium to high production rates. Flex decking does not only provide the highest flexibility possible during construction and production, it is also easy to move or relocate. Thanks to its flexibility the system is highly suitable for mixed production of different models, powertrains and segments and is therefore able to cope with all new trends and fast changing production lines in the automotive industry.
→ Flex decking is designed for the automatic assembly of car bodies with their mechanical parts and eventually batteries, in case of the new electrical vehicles. It can be fully automatic or combine highly automated systems with servo-assisted manual workstations, where ergonomic standards for the operators are always held in the highest consideration.
The final assembly line is self-supporting and modular. Each module is equipped with the handling systems and conveyor technology required for the respective working process. This allows the greatest possible adaptation to individual customer requirements, like implementing, reducing or modifying it by adding or removing modules. In this concept, every module houses a workstation, where all car assembly operations take place.
CPM S.p.A.
The Dürr subsidiary → CPM S.p.A. specializes in turnkey solutions for complete final assembly plants in the automotive and aerospace sectors as well as industry in general.
The structuring on levels offers the best performance with the smallest footprint, especially in the countries where the costs for industrial lands are high. Using elevators and our conveyor technology, the pallets carrying the mechanical parts of the car ready for assembly can be easily moved from one floor to another.
NEXT.assembly is Dürr’s new final assembly strategy which combines all final assembly technologies and processes into a powerful one-stop-shop. Read more about NEXT.assembly in the info box.
NEXT.assembly: Combined technical expertise from Dürr for an efficient final assembly of the future
Dürr’s NEXT.assembly provides customers around the world with processes and technologies for optimized final assembly solutions, enabling them to manufacture their vehicles as efficiently as possible.
NEXT.assembly is the most comprehensive service on the market: Dürr is a one-stop shop for efficient solutions ranging from initial concept planning, consulting and the implementation of individual processes in adhesive bonding technology and in conveyor, assembly, filling and test systems to process-optimized plants. With NEXT.assembly Dürr uses synergies at all levels and increases value with the help of intelligent, networked processes.
How does flex decking work in detail?
Light deck
Light deck is the new generation of flex decking, which is the perfect solution for low to medium production rates. Unlike the traditional flex decking, it is designed on one level, being therefore also suitable to plants with reduced heights. → Light deck is a flexible and modular system, whose transit stations can be easily converted to working stations if production requirements change over time. It is compatible with any type of conveyor (either TTS® or traditional ones) and in case of line modifications it does not require special foundations or civil works, since its structure is self-supporting.
In combination with the advanced technology of ProFleet, the new AGV system for general assembly, light deck reaches its full potential.